When Saros 10R wheels encounter suspension, remote intervention requires leveraging available rig control systems and data streams. Follow these expert procedures:
Immediate Remote Diagnostics & Assessment
- Access Real-Time Rig Control System (RCS): Immediately connect to the rig's data acquisition system. Focus on the Suspension Status telemetry feed.
- Verify Actual Suspension State: Cross-reference multiple indicators:
- Suspension Status Code (e.g., SUSPENDED, FAULT)
- Individual wheel hydraulic pressure sensor readings
- Height sensor feedback
- PLC I/O status for suspension solenoids
- Identify Suspension Trigger: Review event logs preceding the suspension flag. Common triggers include pressure deviations, loss of position feedback, or interlock violations (e.g., motion commands while locked).
Targeted Remote Resolution Actions
Based on diagnostic findings:
- False Trigger/Soft Lock:
- If diagnostics suggest a transient fault or sensor glitch, command a suspension reset sequence through the RCS interface.
- Monitor pressure rebuild and height stability during reactivation.
- Hydraulic Pressure Anomaly:
- Correlate hydraulic manifold feedback (pressure sensors).
- Attempt controlled repressurization of the affected wheel suspension circuit via RCS commands. Initiate a slow, monitored purge cycle if air ingress is suspected.
- PLC State Mismatch:
- Verify the logic state in the wheels PLC. Override any erroneous interlock flags preventing unsuspension via the PLC interface (requires appropriate access level).
- Force a controlled suspension release sequence while ensuring all mechanical safety locks are disengaged (confirmed via telemetry).
Critical Remote Operational Constraints
- Prioritize Rig Stability: Only attempt unsuspension commands if the substructure and load path are confirmed stable and within design limits.
- Confirm Lock Status: Never override suspension if mechanical wheel locks (e.g., pin locks, scissor locks) are indicated as engaged. This requires physical verification.
- Strict Supervision: Any remote override must occur under constant real-time monitoring of pressures, positions, and structural loads. Abort immediately upon unexpected deviations.
Essential Advisory: Successful remote resolution indicates recoverability but does not eliminate the root cause. Implement continuous monitoring of suspension system parameters. Schedule immediate physical inspection, sensor calibration, and potential hydraulic system maintenance upon next access.
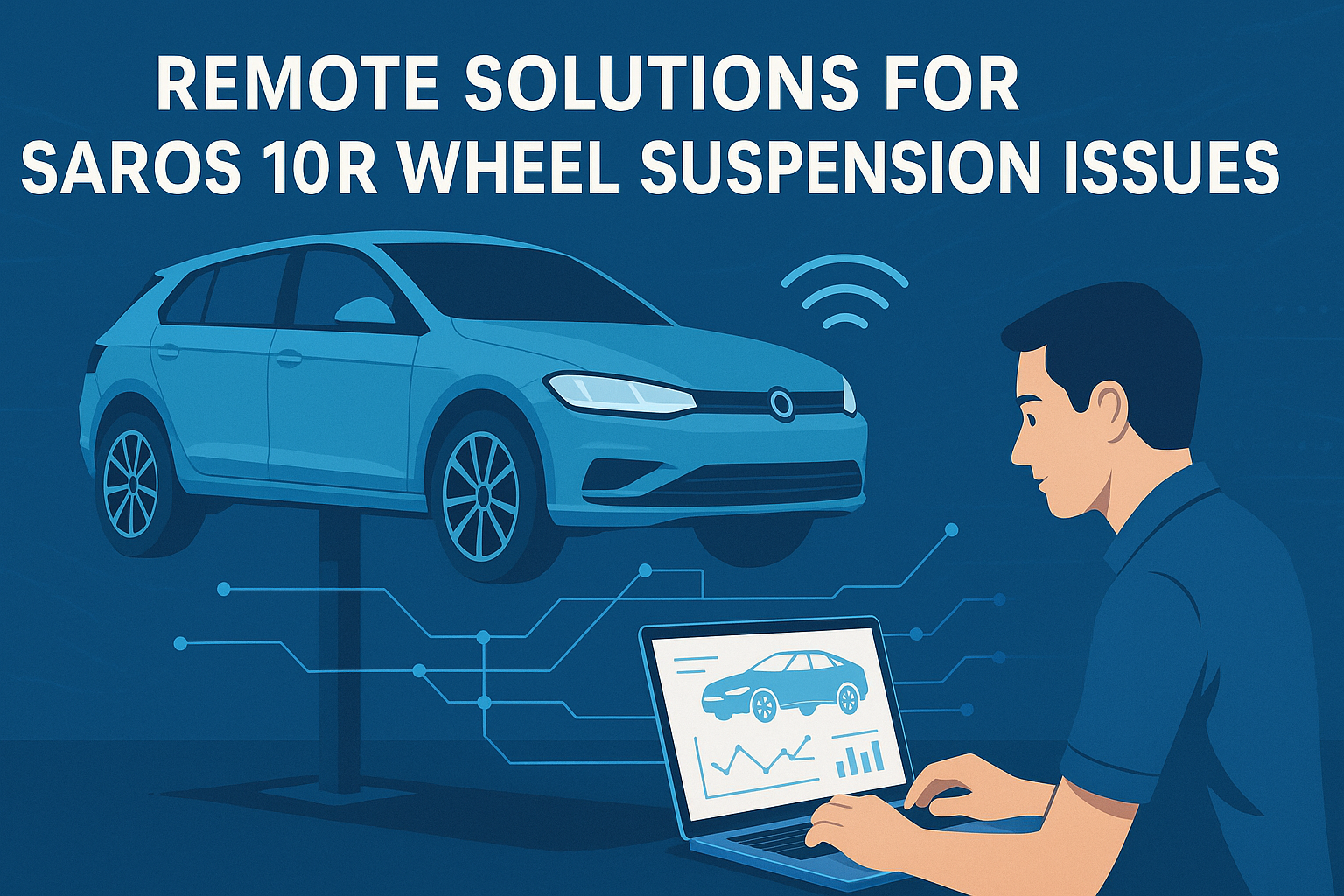